EDM Wire Cutting Machine
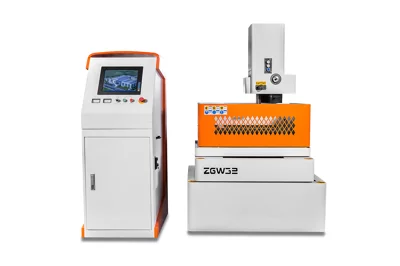
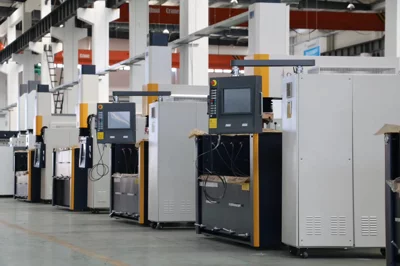
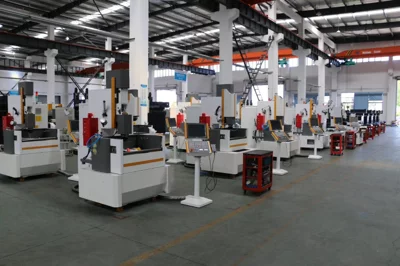
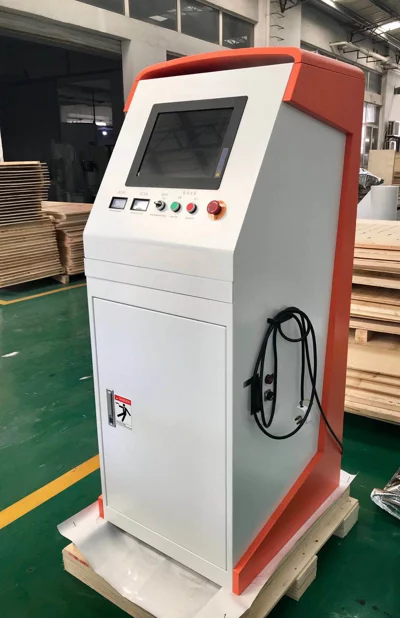
Models List
-
ZGW32
-
ZGW40
- Precision Panasonic servo motor encoder feedback to achieve pitch compensation.
- AC servo motor drive for precise feedback compensation from processing to the end of processing.
- Advanced professional system.
- Full support for ISO Codes.
- Excellent NC Programming Orbit moving from CAD, CAXA drawing directly.
- Digital pulse generator with finish cutting.
Standard cutting samples:
Big taper device cutting samples.
NC Controller:
Industry PC from Advantech Taiwan configuration:
- ICA-6806/681-400
- 128M SD
- Ethernet interface 10/100Mb
- RS232
- USB interface
- Floppy drive
- Keyboard
- Mouse
- 15" LCD
Background editing and program running, thus making it possible to edit a program while the machine is working.
Graphic display online machining trace and workpiece profile.
Automatic graphic edit and program generation.
Translate AutoCAD files to program automatically.
ISO standard G code programming, compatible with 3B code.
HF program and control system features:
- Graphic edit based on AutoCAD, easy to learn and use rapidly and correctly.
- Advanced e-Function, connects machine to Ethernet for optimized resource management and paperless operation.
- English operation menus covering all aspects of WEDM machining technology, including electrical and mechanical presetting, parameter selection, and erosion parameters.
- Comprehensive parameter tables for different materials.
- Efficient workflow rules and peripherals for quick and high-quality workpiece production.
NC system capabilities:
- Simultaneous programming and machining.
- All operations can be performed via mouse clicks.
- Online machining trace display.
- 4-axis interpolation in 3 dimensions with automatic backlash compensation.
- Automatic data save and restore after power outage.
- Automatic home point, edge positioning, and workpiece center finding.
- Step movement for each axis.
- Drawing manipulation: rotate, zoom, mirror.
- Program reverse cut and alarm message display.
- Start working at any code line.
- Batch machining of identical workpieces.
- Backlash compensation.
- Wire lag elimination in high-speed cutting, especially for sharp angles.
- All program and control functions displayed on screen.
- Automatic program generation from AutoCAD files.
- ISO standard G code programming, compatible with 3B code.
- Automatic machine shutdown after program completion.
- Multi-cutting function.
- Automatic reverse run on short circuit.
- Wire break protection function.
- Linear and circular interpolation.
Additional Features:
- High precision ball scales and guides for rapid, smooth, and accurate movement response.
- Self-service lubrication system in pulley bearings to extend bearing life.
- Anti-wave device in wire running system for improved machining precision and extended wire life.
- Moveable clamps on worktable slides for time-saving workpiece installation.
- Integrated lubrication system in all movable parts.
- Constant force wire running structure for optimal finishing results.
- New machine body design with low, wide basement for improved stiffness and stability, built from high-quality cast iron.
- AC servo motors or step motors directly connected to ball screws for stable machine operation.
- Advanced frequency conversion technology for smooth and adjustable wire speed control.
- High-performance pulse generator for efficient machining of various materials, including alloy steels, aluminum alloys, copper, titanium, carbide, ultra-hard materials, conductive materials, and high-temperature materials.
- Anti-stripe erosion technology in generator for superior surface finishing.
- Two patented taper structures: 1) Big taper structure composed of 4 link bars. 2) Precision small taper structure with planetary movement, ensuring vertical alignment of wire and pulley for precise taper cutting.
- Modular design of power generator, NC system, and electrical equipment optimized to resist electromagnetic interference.
- Rigorous testing and inspection of each machine before sale, including 100 hours of continuous full-load testing and 100 hours of non-continuous peak-load testing.
Item | ZGW32 | ZGW40 |
---|---|---|
Worktable Dimension mm | 890 x 760 | 883 x 575 |
Worktable Travel mm | 400 x 500 | 320 x 400 |
Max Cutting Thickness mm | 260 | 260 |
Max Load Weight kg | 400 | 300 |
Machine Weight kg | 1700 | 1600 |
External Dimension mm | 1680 x 1470 x 1800 | 1600 x 1330 x 1800 |
Max Cutting Taper degrees | ± 3 | ± 3 |
Max Cutting Speed mm²/min | ≥ 180 | ≥ 180 |
Best Surface Roughness µm | Rα ≤ 0.8 | Rα ≤ 0.8 |
Electrode Wire Dimension mm | 0.10-0.25 | 0.10-0.25 |
Worktable Minimum Feed mm | 0.001 | 0.001 |
Machining Precision mm | 0.006 (Φ15, thickness 25) | 0.006 (Φ15, thickness 25) |